Такие данные озвучил в ходе заседания Президиума РАН 29
марта доктор технических наук, заместитель директора по научной работе Федерального
исследовательского центра «Институт катализа им Г.К. Борескова» Сибирского отделения
Российской академии наук Александр Носков.
Объем производимой в России продукции на основе катализаторов
составляет 5-6 трлн рублей в год. «В
области нефтепереработки и нефтехимии практически все процессы базируются на использовании
катализаторов, в химической промышленности – подавляющее большинство. Катализаторы
используются и в масло-жировой промышленности (производство маргарина и
спецжиров), а также в фармацевтике (производство субстанций)», - пояснил
Александр Носков.
При этом анализ показал, что импортозависимость российской
нефтепереработки и нефтехимии наиболее велика в процессах, которые были созданы
сравнительно недавно, или в конце XX века. В процессах, запущенных в
середине XX века превалируют отечественные катализаторы, отметил выступающий.
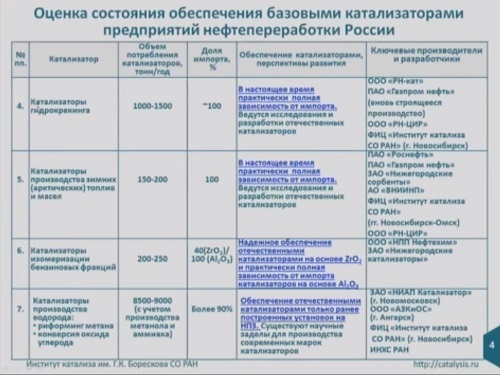
Весьма успешно складывается проблема с производством
катализаторов крекинга тяжелых нефтяных фракций. Этот катализатор представляет
собой сложную композиционную систему, где каждый компонент выполняет свою
функцию.
«В настоящее время благодаря наличию компетенций – ранее это
был Институт проблем переработки углеводородов, сейчас это Центр новых
химических технологий объединенного института катализа в Омске, усилиями
исследовательского центра «КНТ Групп» (Башкортостан) разработана широкая
номенклатура катализаторов различного назначения. Имеющиеся мощности уже
позволяют в значительной степени преодолеть зависимость от импорта - обеспечение
отечественными катализаторами составляют 70%, к 2025 году планирует полностью
перейти на отечественные катализаторы», - сказал Александр Носков. В частности,
в 2022 году «Газпромнефть» планирует запустить новое производство – завод «Газпромнефть
– Каталитические системы» (г. Омск).
Аналогичная ситуация с катализаторами риформинга бензинового
сырья. Как рассказал Александр Носков, над этой проблемой работают две
высококвалифицированных команды - Центр новых химических технологий объединенного
института катализа в Омске и ООО «НПП Нефтехим» (г. Краснодар). «В этом направлении
импортозамещение движется чуть медленнее, что связано со сроком службы: если
катализатор крекинга является постоянно расходуемым, то здесь замена
катализатора происходит раз в 5-6 лет. И по мере вывода из эксплуатации
импортных катализаторов они будут заменяться на российские. Обеспечение отечественными
катализаторами сейчас составляет 50% с плановым увеличением до 70-80% к 2025
году», - озвучил прогноз Александр Носков.
Несмотря на то, что сейчас в области получения высококачественных
дизельных топлив, моторных топлив в целом проблема очистки от соединений серы и
азота пока решается с использованием импортных катализаторов, набор компетенций
в институтах Академии наук, в высших
учебных заведениях, в отраслевых исследовательских структурах «Газпромнефти», «Роснефти»
позволяет прогнозировать, что в ближайшие годы фактически появится
производственная база отечественных катализаторов для замены импортных, отметил
выступающий.
Сложнее обстоит ситуация с катализаторами гидрокрекинга. Приходится
решать задачу получения из нетекучего
материала – фактически из смолы – дизельного топлива. «Сложность задачи можно
охарактеризовать одной цифрой – в ходе этого процесса нужно понизить содержание
серы – от сырья к продукту – в 10 тыс. раз», - пояснил Александр Носков.
Еще одна достаточно сложная проблема связана с катализаторами
полимеризации. «Отечественными научными организациями разработана вся
номенклатура катализаторов, которые необходимы для современных производств. Это
самый массовый титан-магниевый катализатор (ТМК), это металлоценовые и постметаллоценовые
катализаторы полимеризации, хромовые катализаторы. Но сложилась удивительная
ситуация: по российским разработкам,
российским исследованиям освоено производство этих катализаторов за рубежом для
крупнейших зарубежных компаний. А в России идет обсуждение – «нужно, не нужно».
Сейчас идут переговоры с некоторыми компаниями о создании мощного производства,
которое бы закрыло потребность в этой области, но весь процесс займет не менее
3-4 лет», - обратил внимание Александр Носков.
Несколько иная ситуация в области катализаторов паровой
конверсии природного газа для получения водорода, здесь, напротив, ощущается
недостаток научных компетенций. «К сожалению,
в этой области у нас недостаточные научные компетенции, чтобы выйти на самый современный
уровень зарубежных аналогов. И мощности, которые есть в России – ООО «НИАП-Катализатор»
(г. Новомосковск) – до 200 тонн/год, и АО «Ангарский завод катализаторов и
органического синтеза» - до 150 тонн/год – производят в 10 раз меньше катализаторов,
чем необходимо для российской промышленности», - привел примеры Александр
Носков. По его мнению, необходимо создание дополнительных мощностей
производства катализаторов в объеме до 4000 тонн/год.
Непросто складывается ситуация и с еще одной стадией
получения водорода – катализаторами для азотной промышленности. Производство водорода
и синтез метанола происходит на единой технологической платформе через «мокрую
химию» - набор компетенций по этому направлению достаточно велик – проблемой
занимаются ООО «НИАП-Катализатор» (г. Новомосковск), ФИЦ «Институт катализа СО
РАН», Институт органической химии РАН, ИНХС РАН.
«Восстановление такого производства - это размещение его на
высвобождающихся мощностях корпорации АО «ТВЭЛ» (Росатом). Тем более, что в
конце XX века на
Ульбинском металлургическом заводе (г. Усть-Каменогорск) при производстве
катализаторов была опробована технология конверсии оксида углерода и синтеза
метанола», - рассказал Александр Носков.
В качестве одной из самых серьезных проблем, требующих
решения, ученый выделил производство необходимых элементов для катализаторов
нефтепереработки и нефтехимии, в частности, производство цеолитов (материалы с
регулярной пористой структурой). «Научный потенциал в институтах и Академии
наук достаточно высокий: разработаны научные основы методов синтеза ряда марок
цеолитов. Однако до промышленности дошел только один образец катализатора. Решение
этой проблемы является одним из ключевых», - сказал Александр Носков.
В своем докладе он также затронул роль катализаторов в
решение проблемы продуктовой безопасности России: «Сейчас в России производится
около 1,5 млн тонн/год жиров из растительного масла путем гидрирования
растительного масла в твердые жиры. Процесс базируется на импортных катализаторах.
А это хлебопекарная промышленность, кондитерская промышленность и так далее».
По словам Александра Носкова, набор научных компетенций в
этой области пока ограничен. «Поскольку эти катализаторы одноразовые, то
решение возможно только в два этапа: первый – освоение технологии регенерации
импортных катализаторов для повторного использования. Это позволит сократить
закупку по импорту в 4-5 раз. Параллельно необходимо в течение 1,5-2 лет
выходить на создание российского производства. Но пока этот проект находится на
самом старте, и стартовый пистолет еще не выстрелил», - подчеркнул Александр
Носков.
Говоря о запросе отечественных компаний на научные
разработки по производству российских катализаторов, Александр Носков поделился
мнением, что компании неизбежно будут двигаться по разным маршрутам. «С одной
стороны, мы должны изыскивать альтернативных поставщиков, но и одновременно
развивать собственные компетенции в этой области. Стоит упомянуть, что
поскольку технологии были приобретены сравнительно недавно, то многие компании
связаны очень жесткими лицензионными ограничениями, вплоть до запрета на
разработку собственных катализаторов», - отметил ученый.